- Overview
- Product Description
- Product Specification
- Packaging
- Reviews From Customers
- Company Profile
- Company Advantage
- FAQ
Basic Info.
Product Description
Tungsten carbide dies are often used in wire drawing industry. Wire drawing is a process that a wire will go through a single or series of drawing dies to reduce the cross section of a wire. The dies are placed in a steel casing with tungsten carbide as inner "nib".
Many years of experience and commitment to research and development enables Miller to offer a range of tungsten carbide grades to meet the drawing requirements for all applications. We can design reasonable compression area angle and sizing area length to reduce the drawing force and friction force, increasing the service life.
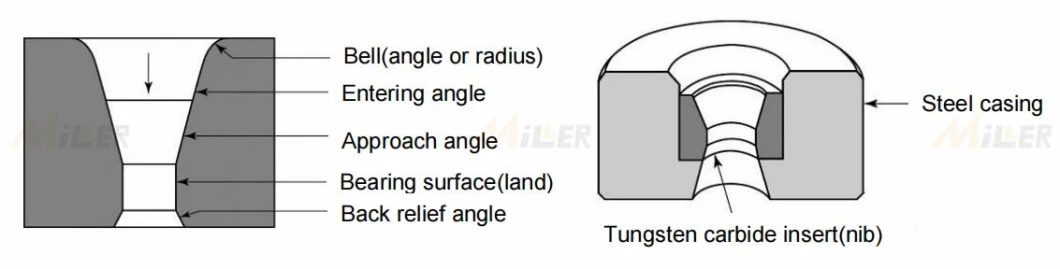
To ensure wire high-quality and control the cost of wire drawing dies effectively, Miller Carbide suggests below 4 aspects:
1) Reasonable collocation of molds: Select proper hole type of the mold, adjust the compression angle appropriately according to the size reduction rate.
2) Wire pretreatment: Cleaning, rust removal, annealing, phosphating etc. to ensure the wire clean.
3) Good lubrication: Select high quality lubricating oil or powder to reduce friction and friction heat effectively.
4) Timely replacement: Repair or replace the mold that reached its service life, to avoid the wire scrap.
ID Size and Tolerance:
ID Size(mm) | Tolerance | ID Size(mm) | Tolerance |
≥0.3~0.4 | -0 /+0.08 | >16.0~24.0 | +0/-0.5 |
≥0.4~0.6 | -0 /+0.08 | >24.0~32.0 | +0/-0.6 |
>0.6~3.0 | -0 /-0.18 | >32.0~40.0 | +0/-0.8 |
>3.0~6.0 | -0 /-0.25 | >40.0~55.0 | +0/-1.2 |
>6.0~9.0 | 0/-0.30 | >55.0~90.0 | +0/-1.5 |
>9.0~16.0 | +0/-0.4 | >90.0 | 0/-2.0 |
OD Size and Tolerance :
OD Size(mm) | Tolerance | OD Size(mm) | Tolerance |
≤10 | -0.15 /+0.15 | >35~40 | -0.4/+0.4 |
>10~16 | -0.2 /+0.2 | >40~45 | -0.5/+0.5 |
>16~30 | -0.3 /+0.3 | >45~50 | -0.6/+0.6 |
>30~35 | -0.4/+0.4 | >50 | -1.3/+1.3 |
H Size(mm) | Tolerance | H Size(mm) | Tolerance |
≤10 | -0.2 /+0.2 | >35~40 | -0.5/+0.5 |
>10~16 | -0.3 /+0.3 | >40~45 | -0.6/+0.6 |
>16~30 | -0.4/+0.4 | >45~50 | -0.8/+0.8 |
Miller Carbide is an experienced manufacturer of tungsten carbide customized parts started from 2008. Our products cover carbide grinding jars & mortars, carbide grinding balls, carbide pegs, carbide static & dynamic rings, bead mill disks, carbide stirring rods, carbide static & dynamic jaws, carbide crusher plates, carbide grinding discs, carbide rotors, carbide roll rings, carbide guide rolls, carbide burrs, carbide sleeves & bushings, and other customized wear-resistant components for valve and pumps ect. With years of tungsten carbide engineering and manufacturing experience, we can concentrate our skills to the development of customized products for a wide spread of wear applications in milling & crushing industry.
Unlike other suppliers, Miller operates with three disciplines: Engineering, manufacturing and after sale service support. This means we are able to improve the efficiency of your machine and tools with customized products and direct access to the manufacturer. Miller Carbide works closely with its customers to ensure their requirements are designed efficiently and suitable for application. We can design the components needed from drawings or delivered samples.
We adhere to the management principles of "quality first, customer first and credit-based" since the establishment of the company and always do our best to satisfy potential needs of our customers. We are sincerely willing to cooperate with enterprises from all over the world in order to realize a win-win situation since the trend of economic globalization has developed with an irresistible force.
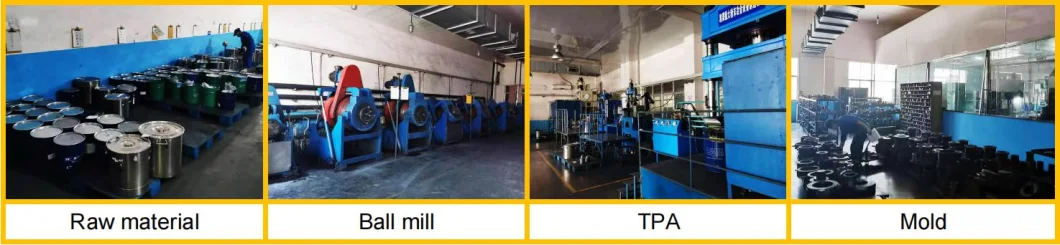
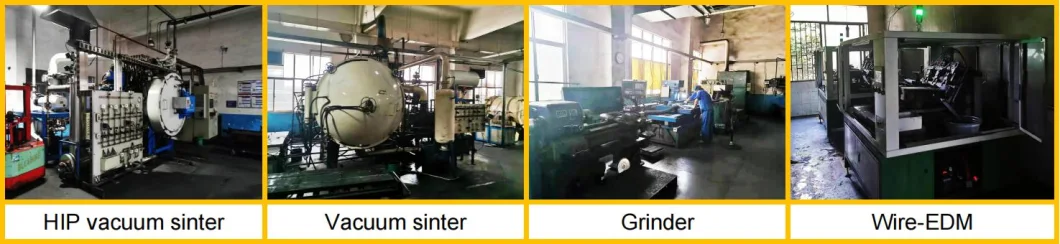
We Offer You These
Direct Sales Integrating R&D, production sales and technology | Mold customization Rich molds OEM customization accepted | Adequate equipment grinding/pressing sintering/deep processing | Technical strength 15 years of experience in technical team, research & innovation |
1. How long is your delivery time?
We can arrange the shipment within 3-5 working days upon receipt of your payment for any sintered blanks stocked items. As for the mass production order or the customized products, we will need 10-30 days production leadtime and indicate the delivery time on the Proforma lnvoice.